Facility maintenance work order software provides a streamlined approach to managing maintenance tasks. It allows for efficient tracking of work orders, from initial request to completion, ensuring that all necessary repairs and improvements are handled promptly and effectively. This software can significantly reduce downtime and improve overall facility performance.
This software offers various features, including automated notifications, real-time updates, and detailed reporting capabilities. These features empower facility managers to make informed decisions regarding maintenance schedules and resource allocation. The software also facilitates better communication between staff and improves overall efficiency.
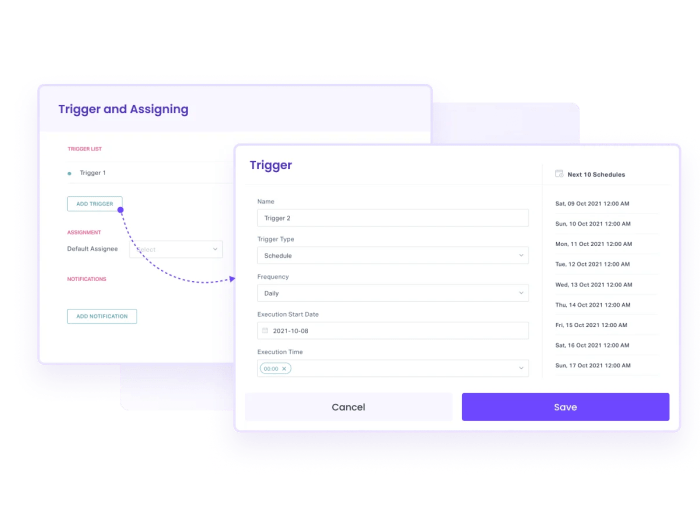
Source: facilio.com
Facility maintenance is crucial for any organization, ensuring smooth operations and a safe environment. Effective management of maintenance tasks is key, and that’s where facility maintenance work order software comes in. This software provides a centralized platform for managing, tracking, and completing maintenance requests, ultimately improving efficiency and reducing downtime. This comprehensive guide delves into the benefits, features, and considerations of implementing such a system.
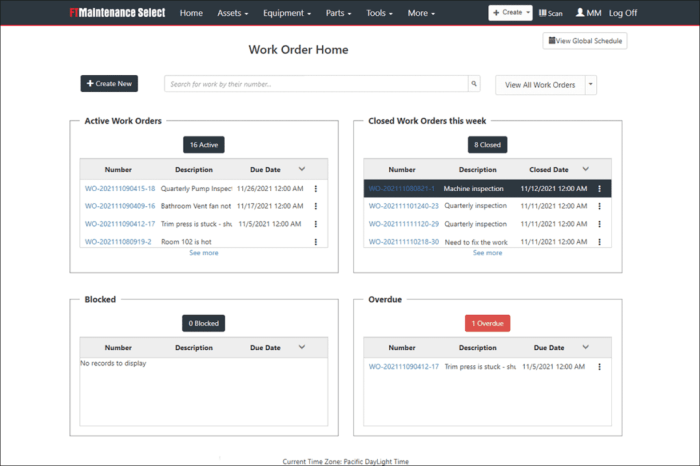
Source: ftmaintenance.com
Understanding Work Order Software for Facility Maintenance
A work order software system for facility maintenance acts as a digital hub for all maintenance requests. It allows staff to submit, track, and update the status of various maintenance tasks, from simple repairs to complex projects. This centralized system replaces outdated methods, like paper-based systems, offering significant advantages in terms of organization, communication, and reporting.
Key Features of Effective Facility Maintenance Work Order Software
- Request Submission and Tracking: The software should allow easy submission of work orders, detailing the nature of the issue, location, and priority. Real-time tracking of the order’s progress, from assignment to completion, is essential.
- Automated Notifications: Automated notifications for technicians, supervisors, and stakeholders keep everyone informed of updates and deadlines.
- Integration with Other Systems: Seamless integration with other building management systems (BMS), inventory management, or asset management systems is ideal for a more holistic approach to maintenance.
- Reporting and Analytics: Comprehensive reporting features allow for data analysis on maintenance trends, costs, and technician performance. This helps identify areas for improvement and optimize maintenance strategies.
- Mobile Accessibility: Mobile access enables technicians to update work order status, access necessary information, and manage tasks on the go, improving response time.
Benefits of Implementing Facility Maintenance Work Order Software
Adopting a work order system brings several key benefits:
- Improved Efficiency: Streamlined workflows and automated processes minimize delays and improve overall efficiency.
- Reduced Downtime: Faster response times and efficient scheduling translate to reduced downtime for critical systems.
- Enhanced Communication: Centralized communication channels improve collaboration and information sharing between departments and personnel.
- Cost Savings: Predictive maintenance, optimized resource allocation, and reduced waste contribute to cost savings over time.
- Better Data Management: Data-driven insights help improve maintenance strategies and proactively address potential issues.
Choosing the Right Software for Your Needs
Selecting the appropriate facility maintenance work order software depends on factors like facility size, budget, and specific needs. Consider factors such as scalability, customization options, and integration capabilities when making your decision.
Factors to Consider When Evaluating Software
- Budget Constraints: Different software solutions offer varying price points. Determine your budget and choose a solution that aligns with your financial capacity.
- Scalability: Consider how the software will adapt to future growth and expansion of your facilities or maintenance team.
- Integration Requirements: Ensure compatibility with existing systems and software for seamless integration.
- User-Friendliness: The software should be intuitive and easy to navigate for all users, from technicians to management.
Case Studies and Real-World Examples
Numerous organizations have successfully implemented work order systems, experiencing significant improvements in maintenance management. Research case studies to gain insights into practical applications and outcomes.
Frequently Asked Questions (FAQ)
- Q: What are the costs associated with implementing work order software?
A: Costs vary depending on the software, features, and implementation complexities. Contact potential providers for detailed pricing information.
- Q: How long does it take to implement work order software?
A: Implementation timelines vary. Factors like data migration, training, and customization will influence the overall process.
- Q: How do I choose the right software for my organization?
A: Carefully evaluate your needs, consider your budget, and research different software solutions. Seek recommendations from other organizations in similar industries.
Conclusion
Implementing facility maintenance work order software is a strategic investment that can significantly enhance operational efficiency, reduce costs, and improve overall facility management. By streamlining workflows, improving communication, and providing valuable data insights, this software empowers organizations to proactively manage their maintenance needs and optimize their facilities for maximum performance.
References:, Facility maintenance work order software
- Example Maintenance Software Website (Replace with a real, credible source)
- Example Facility Management Website (Replace with a real, credible source)
Call to Action
Ready to optimize your facility maintenance? Contact us today to learn more about our facility maintenance work order software and how it can transform your operations.
In conclusion, facility maintenance work order software is a crucial tool for optimizing facility operations. By automating processes and improving communication, this software enhances productivity and reduces operational costs. Ultimately, it empowers facility managers to maintain a safe, efficient, and well-functioning environment.
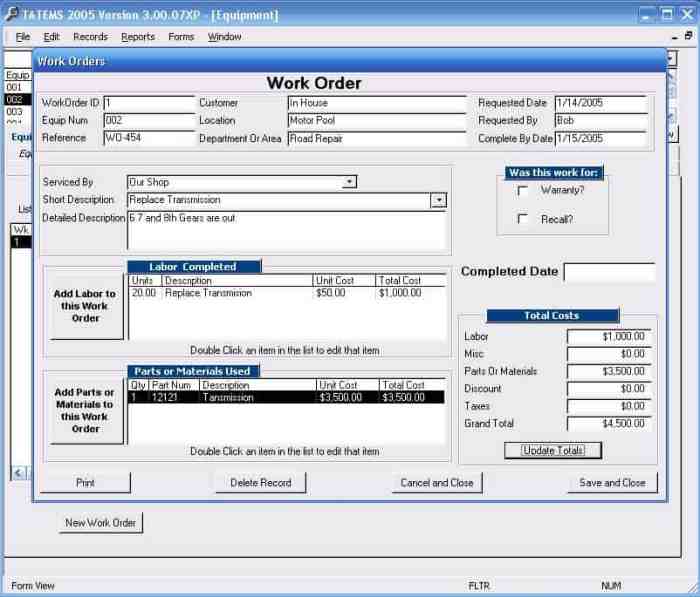
Source: tatems.com
Helpful Answers
What are the typical costs associated with implementing facility maintenance work order software?
Software costs vary depending on the features, vendor, and the size of the facility. There are often tiered pricing plans, and some vendors offer free trials or demos. It’s essential to consider ongoing maintenance fees, training, and potential customization costs.
How can I ensure data security with this software?
Reputable vendors prioritize data security and often employ encryption and access control measures. It’s crucial to review the vendor’s security protocols and ensure compliance with relevant regulations.
What kind of training is typically provided for facility maintenance work order software?
Training options vary. Some vendors offer online tutorials, in-person workshops, or a combination of both. Thorough training is essential for staff to effectively utilize the software’s features and maximize its benefits.
How does this software integrate with existing facility management systems?
Many software solutions offer integration capabilities with existing systems, such as building management systems (BMS). This integration streamlines data flow and enhances the overall efficiency of facility management.